Spaceshot
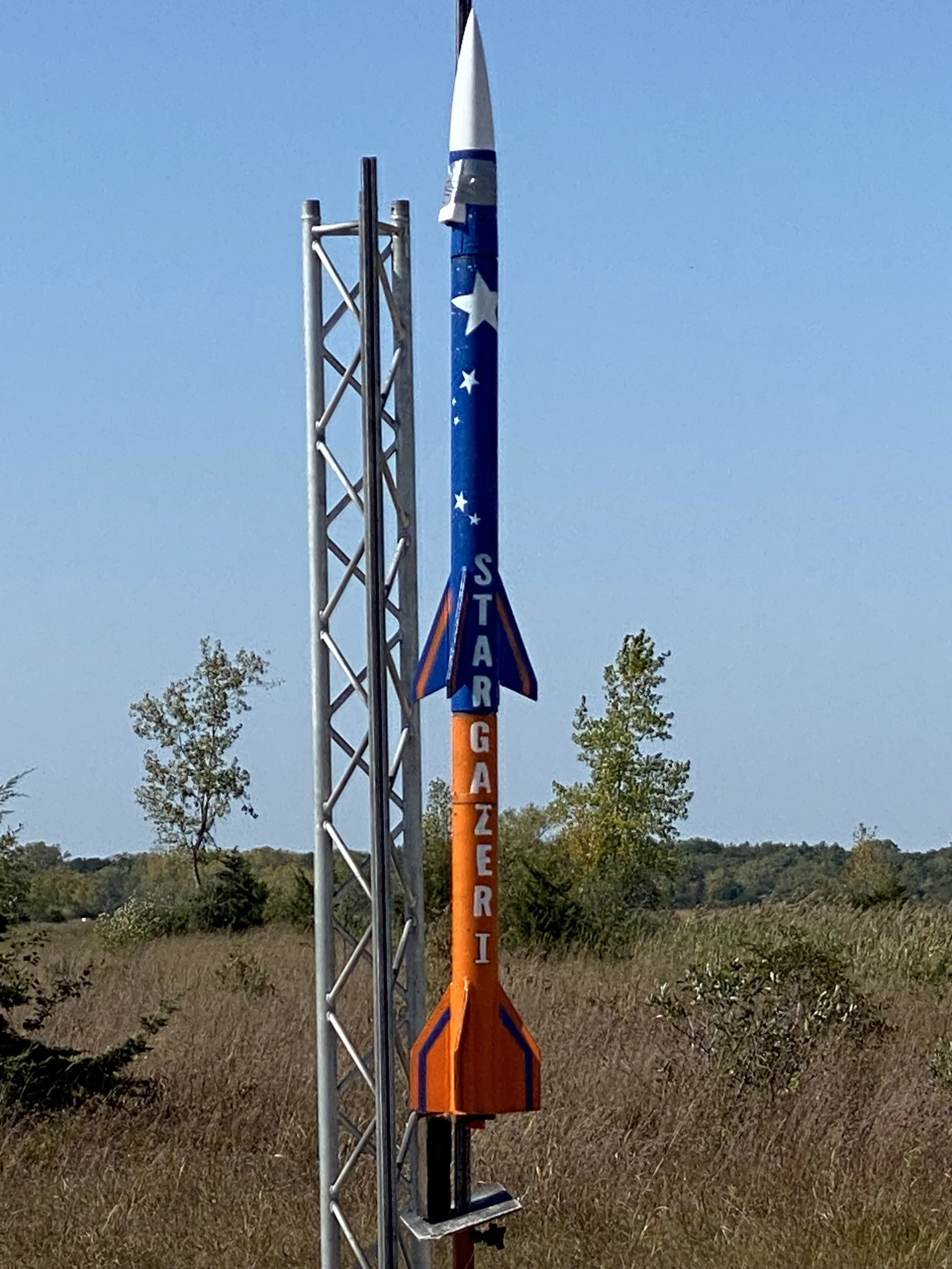

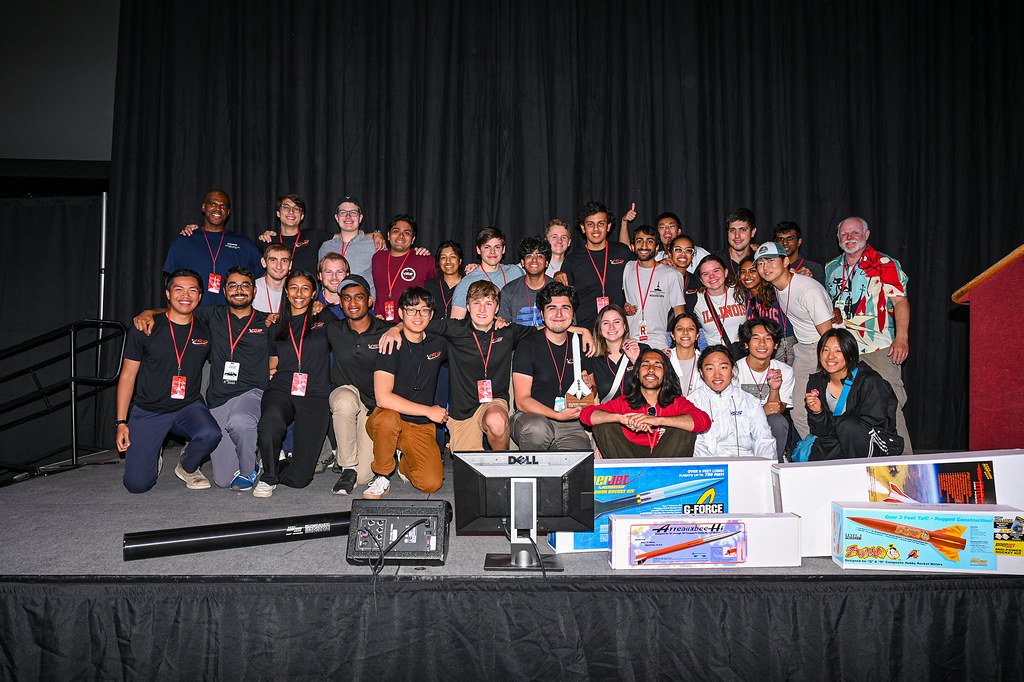
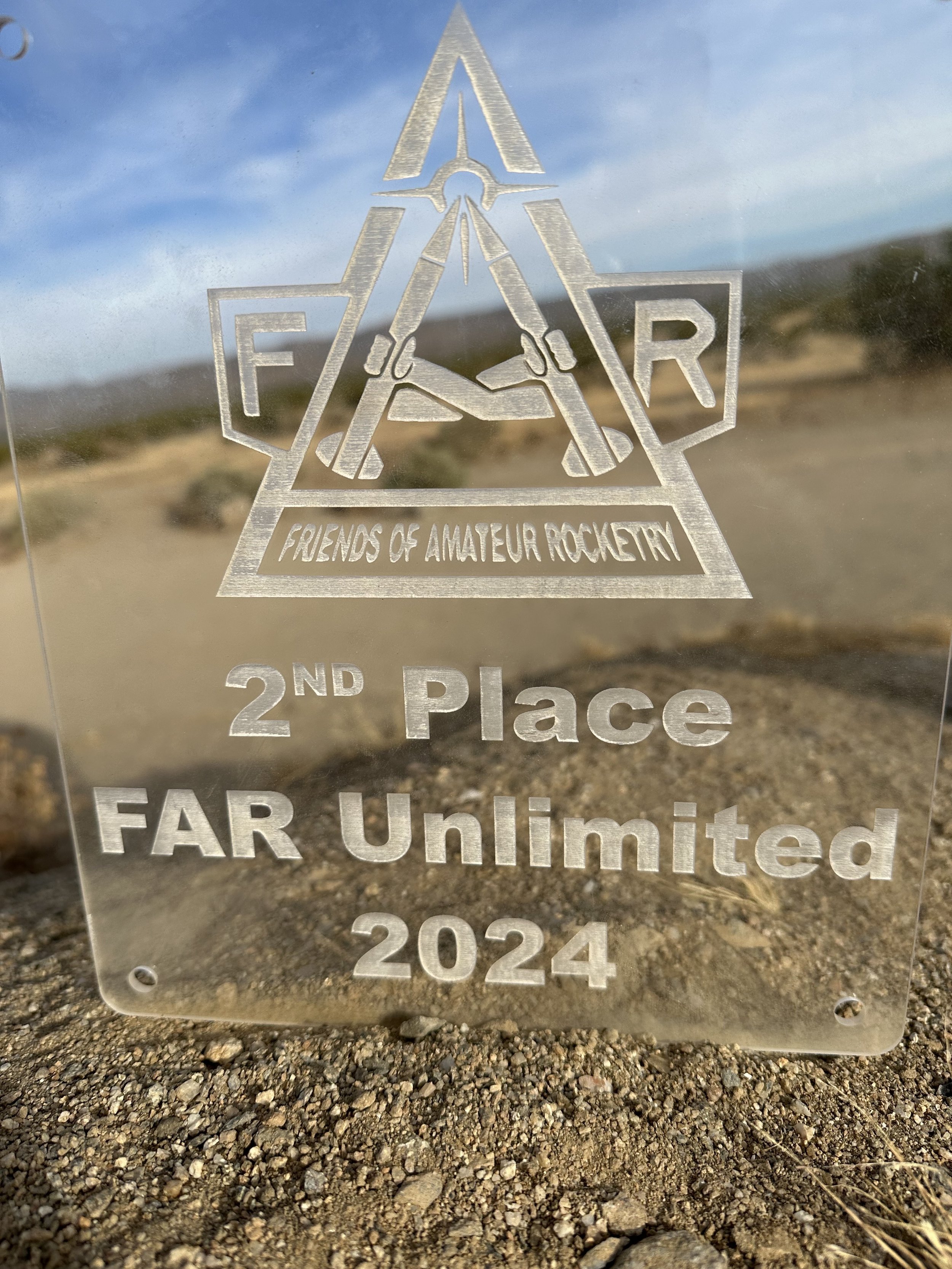
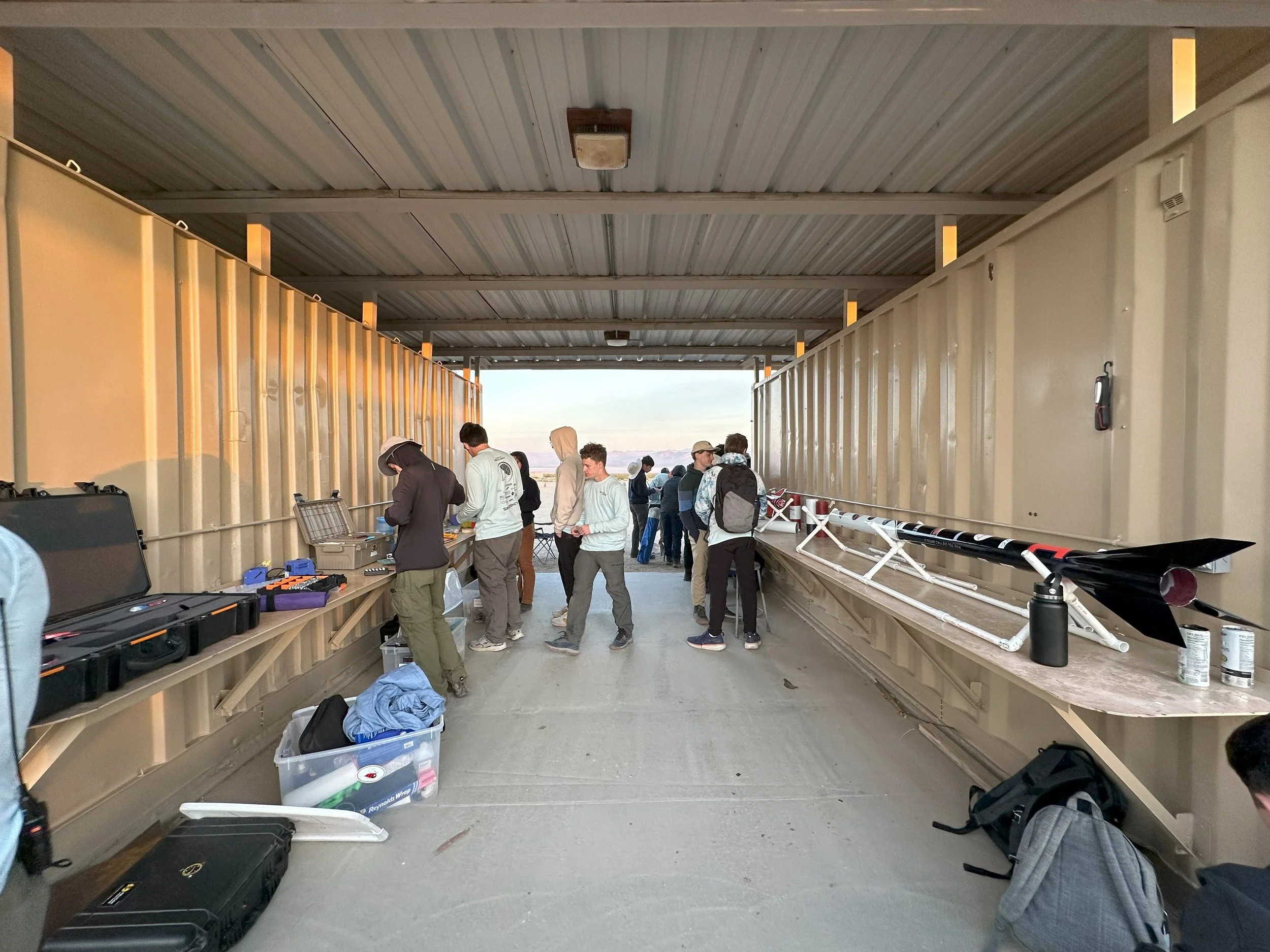
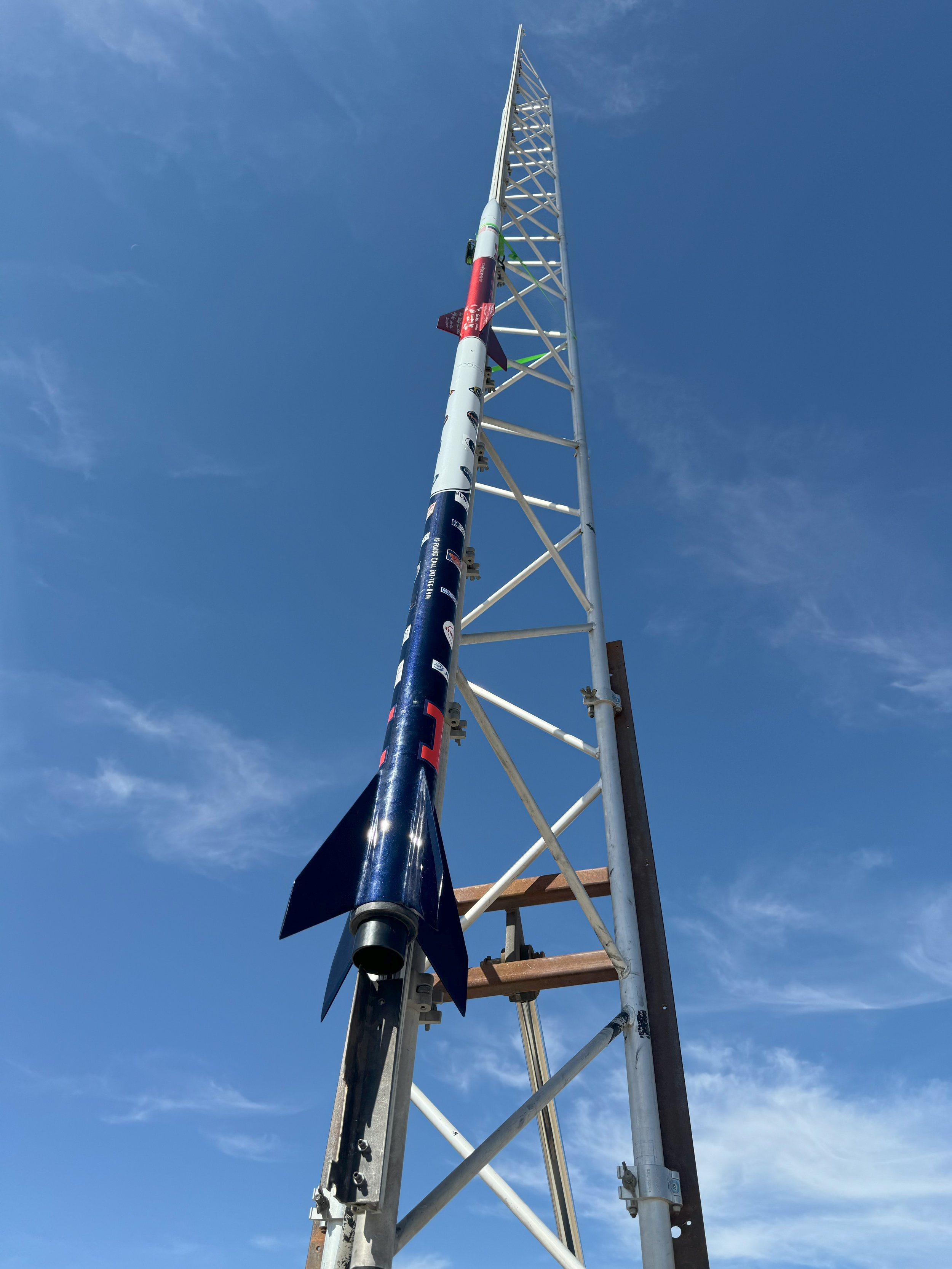
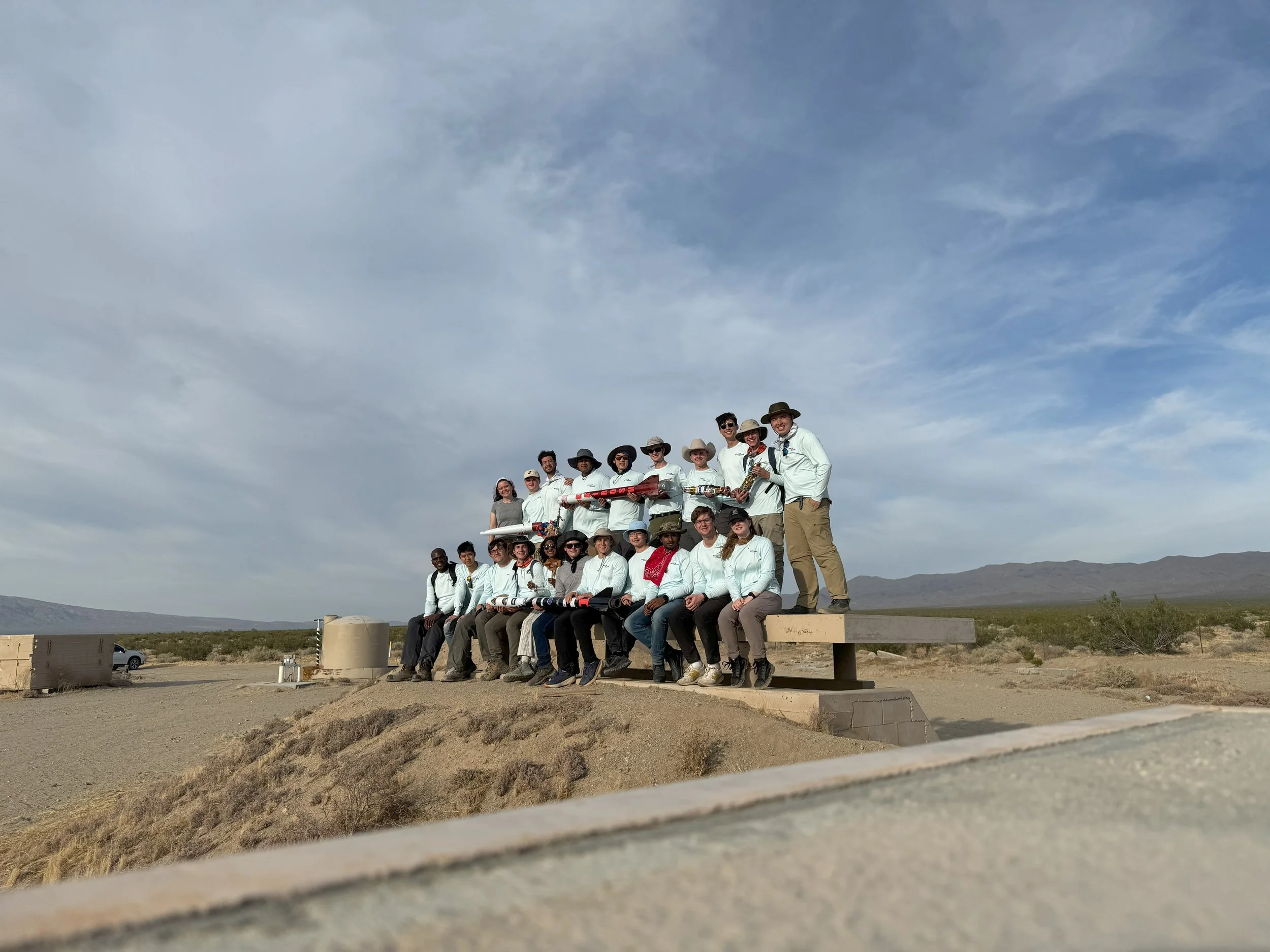
Who We Are:
The rocketry program at the Illinois Space Society is our largest technical project. Its main goal is Spaceshot, a multi-year project dedicated to developing a rocket capable of reaching the Karman line. This journey is split into multiple competitions and projects that work together to expand the technical and engineering capabilities of the team.
In 2023-2024, the rocketry team is launching a 2-stage rocket projected to achieve approximately 100k ft in the unlimited altitude division of FAR-51025 (Friends of Amateur Rocketry-51025). This is a competition in Mojave Desert, California that awards points based primarily on altitude. The goal of this year is to develop multi-stage rocketry capabilities that will aid us in our goal of reaching the Karman line through staging.
ISS has previously participated in the Spaceport America Cup, formally known as the Intercollegiate Rocket Engineering Competition (IREC), for which Intrepid III was launched. Following Intrepid I and Intrepid II, the final iteration of the IREC rocket consisted of a carbon fiber airframe, SRAD (Student Researched and Designed) nose cone, advanced fin retention, a student-designed avionics stack, altitude control using air brakes, parachute reefing, and a CO2 ejection system. After making further improvements using data from two test launches, in July 2023, Intrepid III took 2nd place in the 30k COTS category!
While Intrepid III was being manufactured, development occurred on Stargazer: Stargazer served as a subscale proof of concept rocket to demonstrate staging mechanics. It featured a simple design using COTS (Commercial Off the Shelf) altimeters and a black powder ejection system. In November 2023, following two failed launches, Stargazer completed the first successful stage attempt in Illinois history with boost, motor ignition, separation, and recovery occurring as predicted!
Spaceshot is divided into 3 main teams—structures, avionics, and recovery—with 6 subteams—Structural Design & Analysis, Fabrication, Electronic Hardware, Guidance Navigation & Control, and Avionics Structures—all of which are led by team and subteam leads.
What We Learn:
The Rocketry Program focuses on teaching the engineering design process. We strive to provide all members with experience on the conception to completion of each rocket and its subprojects. We utilize software like NX, OpenRocket, Ansys, Python, and KiCAD for development and later dive into hands-on manufacturing. Additionally, we learn soft skills through direct experience, such as technical writing, presenting, and research. Staging is a highly advanced and sophisticated process; with that, this year introduces many new design considerations and challenges. The focus is engineering creative solutions to ensure maximum success in a project that inherently has numerous modes of failure across every system.
Why YOU Should Join:
Leading a team of students towards an engineering goal is a unique experience, and there are numerous leadership opportunities in the project. Although leadership is selected over the summer, there is no priority on seniority. In fact, out of 10 team/subteam positions this year, 5 selected were sophomores.
Beyond leadership, Rocketry members are given ownership and autonomy in projects. This allows you to build a body of work, and be an expert in various skills. This experience is extremely valuable in pursuing internships and jobs, as you will have applied hands-on experience. Many legacy members of the team have gotten amazing job opportunities due to their work in the team. Additionally, rocketry enables you to gain exposure to the aerospace curriculum early on. Our members, even in other majors, such as ECE and CS, have gained curriculum knowledge. If you are part of a different major, joining rocketry allows you to break into the space industry early on.
Spaceshot is a supportive community and network. Alumni of the program stay socially involved even after graduation, and there is active mentorship within the program.
Leadership
-
Peter Giannetos
Spaceshot Lead
-
Michael Karpov
Avionics Lead
-
Cameron Steelberg
Recovery Lead
-
Ashley Sawa
Structures Lead
-
Surag Nuthulapaty
Operations Lead